Les bonnes recettes de la métallurgie pour la fabrication 3D d’implants médicaux innovants
Des chimistes du CNRS se sont associés à l’entreprise bretonne SLS-France pour concevoir de nouveaux alliages à base de titane parfaitement biocompatibles et bien mieux adaptés aux implants chirurgicaux que les alliages actuels. Leur méthode, qui a récemment fait l’objet d’un brevet et de deux publications scientifiques, consiste à utiliser la fabrication additive à partir de poudres pour obtenir des dispositifs sur-mesure au plus proche de la morphologie des patients.
Prothèses, implants dentaires, agrafes orthopédiques, stents cardiovasculaires…, les implants métalliques sont largement utilisés pour réparer le corps humain. Malgré leurs atouts, ils présentent des failles difficilement remédiables comme la perte de biocompatibilité sur le long terme, une trop grande rigidité par rapport à la matière qui les entoure ou le manque de souplesse dans leur design et leur fabrication. Des matériaux très étudiés qui seraient bien plus adaptés sont les alliages de titane contenant des éléments biocompatibles comme le niobium, le tantale et le zirconium. En effet, ces alliages possèdent des modules d’élasticité très faibles, proches de celui de l’os, et permettent d’éviter la résorption osseuse (l’os qui se retire) en pourtour d’implant et l’échec de l’implantation. Cependant, les tentatives de les fabriquer par technologie additive pour obtenir des dispositifs aux formes et designs extrêmement complexes restent encore très marginales. La fusion laser sur lit de poudre,* par exemple, se révèle particulièrement intéressante pour obtenir des implants chirurgicaux métalliques sur mesure et au plus proche de la morphologie des patients à partir de scans traités via des logiciels de segmentation numériques. Cette technologie additive utilise des poudres pré-alliées qui, pour des compositions « exotiques », nécessitent la mise en œuvre de techniques d’atomisation coûteuses et fastidieuses qui représentent un verrou technologique important.
Pour lever ce verrou, des métallurgistes de l’Institut des sciences chimiques de Rennes, en collaboration avec l’entreprise SLS-France, ont mis au point un mode de fabrication original, dit « in-situ », consistant à utiliser un mélange de poudres élémentaires commercialement pures pour réaliser l’alliage des différents éléments au moment de la fusion par le balayage laser. Ce mode de fabrication, associé à des choix de compositions d’alliages optimisées, a fait l’objet d’un brevet déposé en 2022. Il permet de contourner l’étape critique d’atomisation de poudres et offre une plus grande flexibilité dans les quantités et les compositions à préparer. Leur étude a débouché sur des alliages denses et homogènes du système Ti-Zr-Nb-Sn très prometteurs. En effet, avec des résistances mécaniques comparables, ces nouveaux alliages présentent des modules de rigidité deux fois moindres que l’alliage de Titane de grade médical actuellement utilisé. De plus, certaines compositions ont démontré une consolidation sous charge assez exceptionnelle en comparaison aux alliages élaborés par des procédés classiques. Ces excellentes propriétés ont pour origine une transformation de phase activée sous l’effet de la contrainte et dont les mécanismes de formation en relation avec la déformation plastique restent encore à élucider.
Forts de ces résultats très prometteurs, le laboratoire et l’entreprise ont décidé de renforcer la synergie qui les unit par la création du laboratoire commun (LabCom) LABIOFAB. Les activités de ce LabCom viseront à prototyper des dispositifs médicaux 3D à partir d’alliages de titane aux compositions optimisées, avec l’objectif, à terme, d’une mise sur le marché de dispositifs implantables plus durables et sans complication pour l’hôte.
*La fusion sur lit de poudre est un processus de fabrication additive dans lequel une source d'énergie telle qu'un laser ou un faisceau d'électrons est utilisée pour fusionner des matériaux particulaires (métaux, céramiques ou polymères) afin de créer un objet tridimensionnel.
Rédacteur: AVR
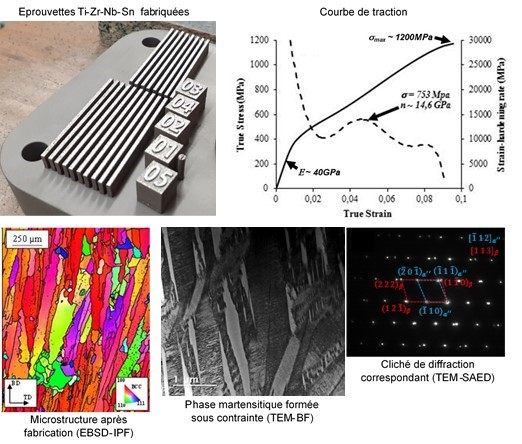
Références
Design of a low Young’s modulus Ti-Zr-Nb-Sn biocompatible alloy by in situ laser powder bed fusion additive manufacturing process
Hugo Schaal, Philippe Castany, Pascal Laheurte, Thierry Gloriant
Journal of Alloys and Compounds 2023
https://doi.org/10.1016/j.jallcom.2023.171539
Outstanding strain-hardening of a new metastable β-titanium alloy elaborated by in situ additive manufacturing L-PBF process
Hugo Schaal, Philippe Castany, Thierry Gloriant
Materials Science and Engineering A 2023
https://doi.org/10.1016/j.msea.2023.145117